Wykrywacze. Detektory metali w przemyśle spożywczym
Zastosowanie detektorów metali gwarantuje absolutną czystość surowców, półproduktów i wyrobów finalnych pod względem zanieczyszczeń metalowych, jednocześnie chroni maszyny produkcyjne przed uszkodzeniami w trakcie prowadzenia procesów przetwórczych.
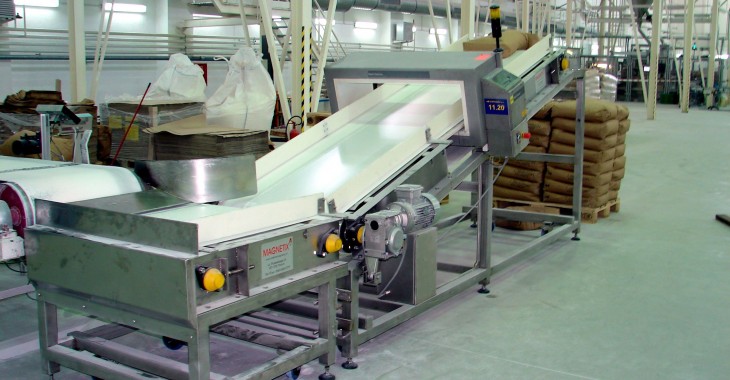
Urządzenia te stanowią gwarancję wytwarzania żywności bez zanieczyszczeń ferromagnetycznych oraz bezpieczną pracę maszyn i urządzeń przetwórczych. Są postrzegane przez większość producentów różnych grup produktów żywnościowych jako zasadniczy element każdego efektywnego systemu kontroli jakości. Skuteczny proces wykrywania metali zapewnia ochronę przed wadliwymi wyrobami i ewentualnym wycofywaniem ich ze sprzedaży, pomaga też zredukować ogólne koszty produkcji.
Obecnie detekcja ciał obcych (zanieczyszczeń ferromagnetycznych), bez względu na branżę spożywczą, staje się coraz bardziej powszechna i pożądana. Zagadnienie to dotyczy zarówno prostych urządzeń montowanych w instalacjach, takich jak filtry, sita, magnesy, jak i tych opartych na nowoczesnej technologii, tj. detektorów lub systemów wykrywania i usuwania zanieczyszczeń metalicznych. Oferowana aktualnie w tym zakresie technika pozwala wykrywać, dzięki zastosowaniu elektronicznych detektorów metalu zanieczyszczenia ferromagnetyczne na różnych etapach produkcji o średnicy nawet poniżej 1 mm. Dotyczy to również surowców i produktów zapakowanych czy zamrożonych. Generalna zasada działania tego typu wykrywaczy polega na zastosowaniu przenikliwego pola, dla którego sam produkt powinien być jak najbardziej obojętny. Z drugiej strony niepożądane zanieczyszczenie powinno intensywnie reagować na zastosowane pole, aby je można było skutecznie usunąć z surowca lub produktu. Największy zakres zastosowania znalazło wykorzystanie pola elektromagnetycznego o określonych zakresach częstotliwości.
Surowce pochodzenia zwierzęcego poddawane w toku produkcji różnorodnym procesom technologicznym narażone są na różne zanieczyszczenia biologiczne, chemiczne i fizyczne, w tym ferromagnetyczne. Wpływ na to mają maszyny, urządzenia, surowce pomocnicze dodawane do produkcji oraz czynnik ludzki. Aby zmniejszyć ryzyko powstania sytuacji, w której zanieczyszczony produkt trafia do klienta, należy prowadzić proces detekcji obejmujący surowce mięsne, półprodukty oraz wyroby gotowe. Detektory lub systemy wykrywania zanieczyszczeń powinny być umieszczone na końcu linii do pakowania produktów lub jak najbliżej końcowego etapu ich pakowania, zgodnie z głównym procesem technologicznym. Detekcji należy poddawać każdą partię produkcyjną i każdą sztukę produktu. W wyniku detekcji następuje automatyczne odrzucenie przez odrzutnik detektora, poza linię, produktów zanieczyszczonych cząsteczkami metali. Ponadto detektory są tak skonstruowane, że wyroby zanieczyszczone, odrzucone przez detektor, wyrzucane są automatycznie do zamykanego kosza, usytuowanego przy detektorze. Jednocześnie podczas wykrycia wyrobu zanieczyszczonego cząstkami metali w detektorze włącza się sygnał alarmowy (dźwięk lub pulsacyjne światło).
Źródła zanieczyszczeń ferromagnetycznych w przemyśle spożywczym
Istnieje wiele źródeł zanieczyszczeń i nawet najbardziej ścisła kontrola nie chroni przed okazjonalnymi incydentami. Stosowanie systemów zarządzania produkcją (Dobra Praktyka Produkcyjna, Dobra Praktyka Higieniczna, system HACCP), w znaczący sposób minimalizuje prawdopodobieństwo przedostawania się cząstek metalu do strumienia wyrobów, a prawidłowa konstrukcja i odpowiedni dobór detektorów metalu zwiększa prawdopodobieństwo ich niezawodnego wykrycia i odrzucenia. Zanieczyszczenia ferromagnetycz
ne zwykle pochodzą z wielu źródeł. Zaliczamy do nich:
• zanieczyszczone surowce rolno-spożywcze (etykietki metalowe, śrut ołowiany w mięsie dziczyzny, kawałki drutu w masie ziarna pszenicy, drut z przesiewaczy podczas czyszczenia i sortowania materiałów ziarnistych i sypkich, części metalowe maszyn i ciągników rolniczych w warzywach, haczyki w złowionych rybach, klamerki i opaski druciane z pojemników metalowych itp.),
• przedmioty i rzeczy osobiste pracowników obsługujących maszyny i linie produkcyjne (metalizowane guziki, długopisy z metalowymi elementami, biżuteria, monety, klucze, spinki do włosów, pinezki, szpilki, spinacze do papieru itp.),
• narzędzia napraw, regulacji i konserwacji maszyn (śrubokręty i podobne narzędzia, opiłki i żużel spawalniczy z napraw, ścinki drutu miedzianego z napraw elektrycznych, różne elementy wynikające z niedostatecznego czyszczenia powierzchni maszyn i urządzeń czy opiłki metalowe z napraw rur stalowych),
• zanieczyszczenia ferromagnetyczne powstające w procesach technologicznych (zanieczyszczenia w postaci opiłek i wiór metalowych powstających w trakcie tarcia elementów maszyn, fragmenty pękniętych sit, odzyskana folia z wyrobów opakowaniowych itp.).
Jednym ze sposobów eliminowania zagrożeń fizycznych (tj. zanieczyszczeń ferromagnetycznych) w procesach produkcyjnych przerobu mięsa jest stosowanie detektorów metali. Ogólna zasada działania tych urządzeń polega na wykrywaniu zmian w polu elektromagnetycznym wywoływanym przez materiały przewodzące lub magnetyczne, które znajdą się w ich pobliżu. Ich zadaniem jest wykrywanie (detekcja) cząstek Fe, Al, Cu, CuSn, Pb, Zn, które w postaci różnych części, elementów maszyn czy opiłek mogą trafiać jako zanieczyszczenia w strefę roboczą maszyn czy do przerabianego surowca, półproduktu, lub wyrobu finalnego. W praktyce przemysłowej urządzenia te stanowią ważny element z zakresie przestrzegania norm ISO9001 względnie zasad i procedur HACCP. Ze względu na różnorodność zanieczyszczeń metalowych, rozpoznanie potencjalnych źródeł zanieczyszczeń stanowi istotny etap opracowania całościowego programu wykrywania metali.
Ogólna charakterystyka i wykorzystanie
Przemysłowy system wykrywania metali służy do wykrywania i odrzucania niepożądanych zanieczyszczeń metalami, co poprawia z jednej strony bezpieczeństwo wytwarzanej żywności, z drugiej zwiększa bezawaryjną pracę maszyn. Typowy system wykrywania metali składa się z czterech głównych podzespołów, tj. cewki wykrywacza lub „głowicy czujnikowej”, interfejsu użytkownika (panelu sterowania), systemu transportowego, automatycznego systemu odrzucania oraz innych, dodatkowych elementów. Większość nowoczesnych wykrywaczy metali dzieli się na dwie główne kategorie. Pierwszy typ wykorzystuje głowicę czujnikową z „cewkami zrównoważonymi”. Detektory o takiej konstrukcji mogą wykrywać wszystkie rodzaje zanieczyszczeń metalowych, w tym metale żelazne, nieżelazne i stal nierdzewną, w wyrobach świeżych i mrożonych. Kontrolowane wyroby mogą być nieopakowane lub opakowane (w tym także w folie metalizowane).
Drugi typ wykrywaczy wykorzystuje magnesy stałe zamontowane w głowicy czujnikowej. Głowice te są w stanie wykrywać metale żelazne i magnetyczne, w tym stale nierdzewne, ale tylko w wyrobach świeżych i mrożonych, zapakowanych w folie aluminiowe. Głowice czujnikowe są oferowane praktycznie we wszystkich rozmiarach, dostosowanych do każdego kontrolowanego wyrobu. Mogą mieć kształt prostokątny lub okrągły i być montowane poziomo, pionowo albo pod kątem. Kolejnym elementem detektora metalu jest interfejs użytkownika, czyli panel sterowania. Stanowi on zasadniczą część elektronicznego systemu sterowania i jest często montowany bezpośrednio na głowicy czujnikowej. Inną częścią roboczą tego systemu są zespoły do przenoszenia wyrobu przez strefę kontroli. Najczęściej są to różnej konstrukcji przenośniki lub plastikowe zsuwnie z wykrywaczem zamontowanym pod kątem czy niemetalowe rury instalowane poziomo lub pionowo. Te ostatnie stosowane są przy kontroli strumienia przemieszczanego surowca lub produktu w postaci proszku czy płynów.
Do urządzeń transportowych często mocowane jest automatyczne urządzenie odrzucające, usuwające zanieczyszczony produkt z linii produkcyjnej. Dostępne są różne typy takich urządzeń, w tym wydmuchowe, wyrzutowe lub zapadniowe itp. Należy dodać, iż typ urządzenia odrzucającego zależy od rodzaju kontrolowanego wyrobu. Oprócz wymienionych, głównych podzespołów systemu wykrywania metali występują też inne istotne elementy systemu. Są to między innymi pojemniki mocowane przy boku przenośnika służące do gromadzenia i przechowywania odrzuconych wyrobów czy zanieczyszczeń, osłony między wykrywaczem a urządzeniem odrzucającym oraz urządzenie awaryjne działające w razie awarii wykrywacza metali. Ponadto, w skład systemu wchodzi urządzenie do potwierdzania odrzucenia, z czujnikami i regulatorami czasowymi i sygnalizator optyczny lub alarm dźwiękowy ostrzegający operatorów o różnych, innych zdarzeniach np. o nadejściu terminu testowania lub zapełnieniu pojemnika na odrzuty.
W przemyśle spożywczym wykorzystywane są różne rodzaje i typy detektorów metali, które w zależności od przyjętego kryterium, branży i specyfiki produkcji dzielą się na różne grupy. I tak w zależności od budowy i przeznaczenia urządzenia te można podzielić:
• separatory nadtaśmowe;
• wykrywacze metalu,
- płaskie,
- tunelowe (dzielone, niepodzielne),
- wykrywacze z tunelem okrągłym;
• bębny magnetyczne i separatory bębnowe;
• sita magnetyczne;
• separatory metali kolorowych;
• chwytaki magnetyczne.
Urządzenia te pracują w zróżnicowanych warunkach środowiskowych i wydzielają (wychwytują) zanieczyszczenia metalowe z różnych surowców czy produktów. Pracują najczęściej w systemie ciągłym i są lokalizowane na tych odcinkach linii technologicznych, w których występuje największe prawdopodobieństwo pojawienia się zanieczyszczeń ferromagnetycznych, a tym samym bezwzględna konieczność ich dokładnego usunięcia.
W praktyce przemysłowej stosowane są detektory metali, których sterowanie odbywa się za pomocą elektronicznych paneli, zapewniających dostęp do wielu funkcji niezbędnych przy prawidłowej kontroli przebiegu procesu technologicznego, jak też jakości produktów. Przemysłowe wykrywacze metali projektowane są tak, aby mogły bezpośrednio lub zdalnie komunikować się z pozostałymi urządzeniami pracującymi w linii technologicznej. Niektóre firmy oferują zarówno detektory (głowice), służące do wbudowywania w już istniejące linie produkcyjne, jak również proponują całe zintegrowane systemy zawierające między innymi detektor, stolik bądź podstawę mocującą, system separacji, elementy transportu określonych produktów oraz pozostałe, niezbędne oprzyrządowanie. Systemy takie pozwalają również na prowadzenie statystyki kontrolowanych produktów, poprzez między innymi zliczanie osobno wszystkich kontrolowanych oraz zanieczyszczonych surowców czy produktów.
Cały artykuł został opublikowany w nr 3/2018 magazynu Kierunek Spożywczy.
Komentarze